- Overview
- Product Description
- Application Scenarios
- Recommend Products
- Customer′s Feedback
- Company Profile
- FAQ
Basic Info.
Packaging & Delivery
Product Description
Surface Treatments G50 Steel Grit Sand Abrasive Sand Shot Blasting Casting Steel Grit Cast Stel Sand
"Casting steel grits" can refer to steel grits that are specifically manufactured for use in the casting industry. Steel grits are abrasive media made from hardened steel and are commonly used in various industrial applications, including casting.The selection of the appropriate size and hardness of casting steel grits depends on the specific requirements of the casting process and the materials being cast. The grits need to be durable enough to withstand the abrasive cleaning process and provide the desired surface finish without damaging the molds or patterns.
Casting steel grits play a vital role in ensuring the quality and consistency of cast products in the casting industry by helping to maintain clean and well-prepared casting surfaces.
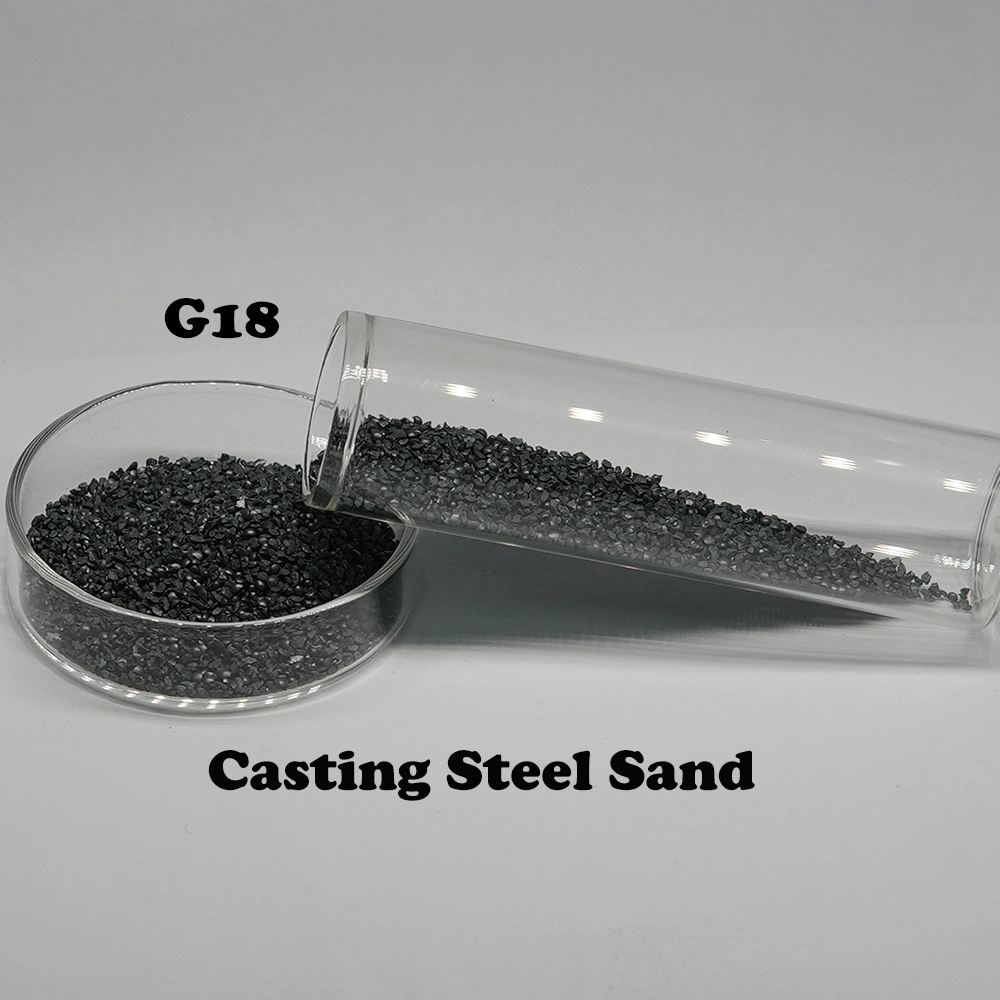
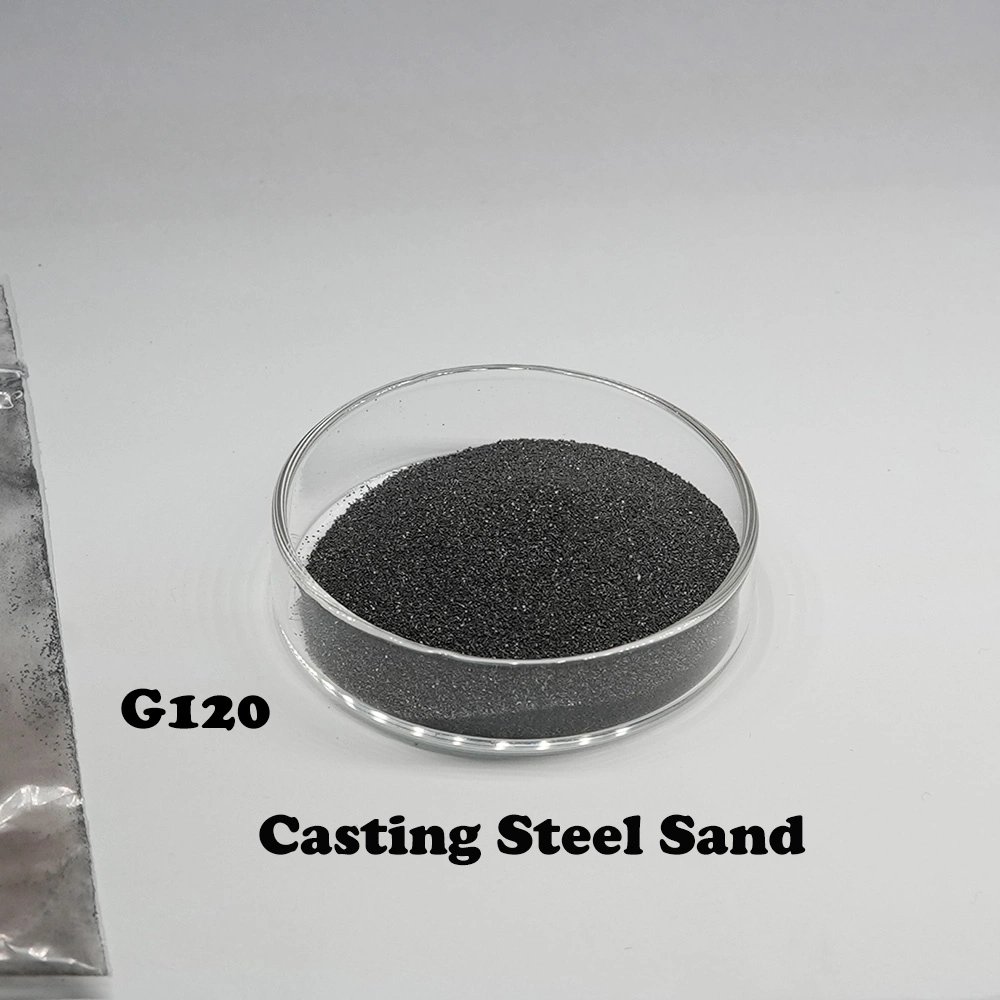
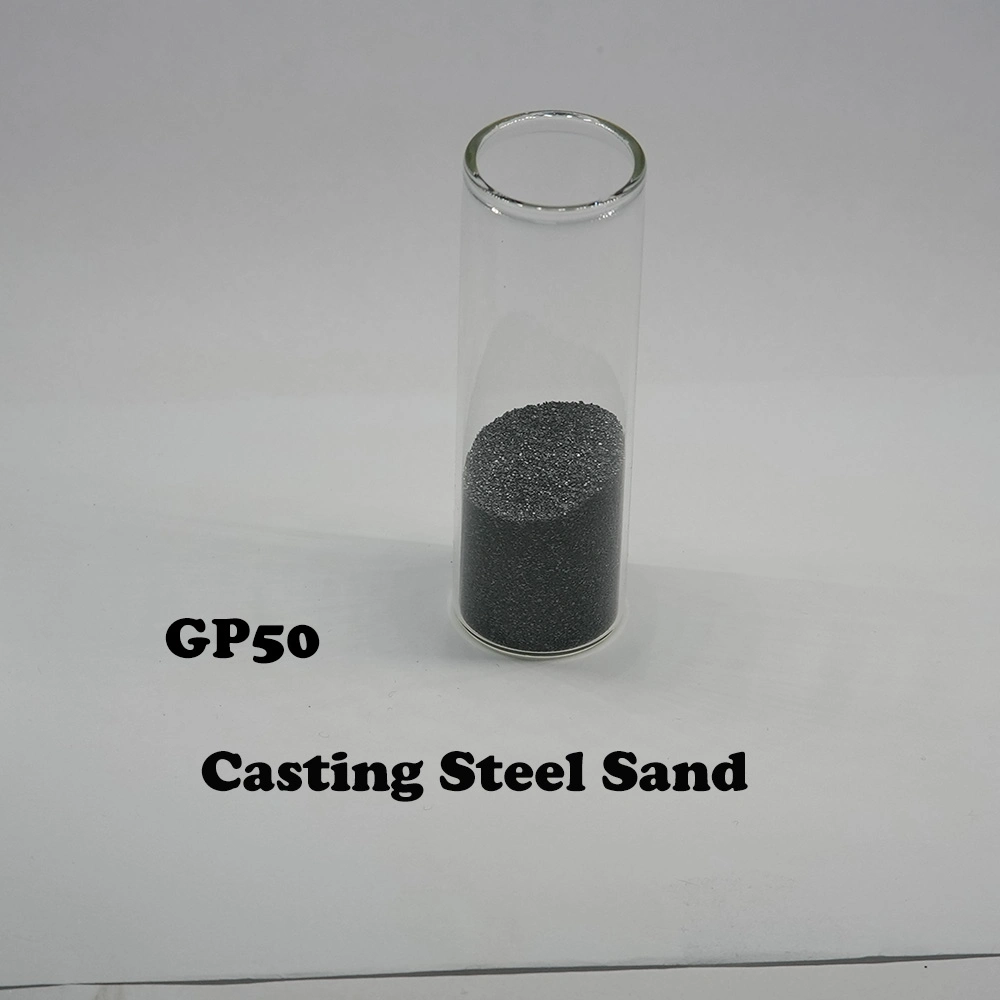
Project | National standard steel grit | High quality steel grit | |
Carbon | 0.85-1.20 | 0.10-0.20 | |
Chemical composition% | Silicon | 0.40-1.20 | 0.10-0.35 |
Manganese | 0.60-1.20 | 0.35-1.50 | |
Sulfur | <0.05 | <0.05 | |
Phosphorus | <0.05 | <0.05 | |
Hardness | GP | HRC46-50 | HRC46-50 |
GL | HRC56-60 | HRC56-60 | |
GH | HRC63-65 | HRC63-65 | |
Density | >7.40g/cm3 | 7.6 g/cm3 |
Foundry and Casting Industry:
- Mold and Core Cleaning: Casting steel grits are used to clean molds and cores before the casting process, ensuring that they are free from contaminants and provide a smooth surface for the molten metal to solidify.
- Shot Blasting: Shot blasting with casting steel grits is used to clean and prepare the surfaces of molds, patterns, and castings. It removes adhering sand, scale, and impurities and can create the desired surface texture for the final cast product.
- Die Casting: In die casting operations, casting steel grits can be employed for mold and die cleaning, maintaining the precision and quality of the castings.
Automotive Industry:
- Surface Preparation: Casting steel grits are used for cleaning and preparing automotive components, such as engine blocks, transmission housings, and suspension parts, before painting, coating, or other finishing processes.
Shipbuilding and Maritime Industry:
- Ship Surface Preparation: Casting steel grits are used to clean and prepare the surfaces of ship hulls, tanks, and other marine components before painting, maintenance, or repair.
Construction Industry:
- Concrete Surface Preparation: In construction, casting steel grits can be used for preparing concrete surfaces, such as bridges, highways, and buildings, before applying coatings or overlays.
Aerospace Industry:
- Aircraft Component Preparation: Casting steel grits are used to prepare and clean critical aerospace components, ensuring the highest standards of surface cleanliness and adhesion for coatings.
General Manufacturing and Metalworking:
- Surface Finishing: Casting steel grits can be used to achieve specific surface finishes on metal components, such as gears, machine parts, and structural steel elements.
- Rust and Coating Removal: They are effective in removing rust, old coatings, and contaminants from metal surfaces.
Bridge and Infrastructure Maintenance:
- Bridge Surface Maintenance: Casting steel grits can be used in the maintenance and refurbishment of bridges and infrastructure, ensuring structural integrity and extending the service life of these assets.
Cleaning and Restoration:
- Historical Restoration: In restoring historical or architectural structures, casting steel grits can help in cleaning and preparing surfaces while preserving the integrity of the original materials.
Marine and Offshore Industry:
- Oil Rig Maintenance: Casting steel grits are used to clean and prepare oil rig components, ensuring they withstand harsh marine conditions.
Mining and Quarrying:
- Rock Surface Cleaning: In mining and quarrying operations, casting steel grits are used to clean rock surfaces to facilitate drilling and blasting.
Founded in 1996, Zhengzhou Xinli Wear-resistant Materials Co. Ltd. Is a professional integrative enterprise specializing in R&D, producing, and selling various wear-resistant materials. Such as white fused alumina, white corundum powder, alumina powder, white aluminum oxide powder, green silicon carbide powder, brown fused alumina, brown corundum powder and other wear-resistant materials. With about 25 years experiences, Zhengzhou Xinli has become the first enterprise that achieves the original crystal granularity to standard 0.3μm, can gain the effect of metal mirror polishing. Xinli Wear-resistant Materials has complete inspection equipment and quality control system, and obtained ISO9001:2015 quality management system certification.
Zhengzhou Xinli Wear-resistant Materials Co. Ltd. Is located in Zhengzhou, Henan Province. With the advanced production equipment and testing instruments, the annual sales quantity of the wear-resistant materials reaches to 3,000 tons. Now, factory equip 3 sets integrated smelting furnace, 2 sets 12000V magnetic extractor, ball mill, barmac, air flow mill shaping machine, and 3 production lines. The wear-resistant materials produced by Xinli are widely used in the sandblasting, grinding and filling of semiconductor, hardware, machinery, electronics, glass and paint industry. Xinli can supply the different standards of the wear-resistant materials, such as PEPA,JIS and ANSI etc. The product quality can take the place of parts of imported materials.
Q: Are you a trading company or manufacturer?
A: We are a manufacturer enterprises of abrasives over 20years.our products have competitive price and quality guarantee. Welcome to send your inquiry!
Q: Do you provide samples ? is it free or extra ?
A: Yes, we could offer the sample for free charge but you need to pay the cost of freight.
Q:How can I get the new price of a product?
A: Please provide the exact or approximate quantity, packing details, destination port or special requirements, then we could give you the price accordingly.
Q:How do you manufacture abrasives?
A:Grinding → Wet classification (granulation) → Drying → Bagging.
Q:Is the quality of the abrasives okay?
A: We have the quality control system ISO9001:2008, and it's been followed strictly. We also have the professional QC team, and each our package worker will be in charge of the final inspection according to the QC instruction before packing.
Q: How long is the lead time?
A: Except OEM products, generally 5-7 days for trial order, 10-20 days for mass order once deposit received.
Q:How about your after-sale service ?
A: If any technical or quality problem after you receive the cargo, you can contact us any time.If the problem caused by us, we will send you free goods for replacement or refund your loss.
Q:What is the price?
A:Please feel free to contact us using the Price / Quotation Request Form as it depends on the quantity, etc.
Q:Can we have a visit to your factory?
A:You're warmly welcoming to visit our plant. And please inform me of your scheduled time in advance, we'll pick you up and arrange the agenda for you.
Q:Do you have any experience with exporting?
A:Yes, We have a global sales network reaching all around the world.
Q:Can I use my own design package?
A:Yes, The package can be with your logo.