Basic Info.
Model NO.
123
Type
Reverberatory Furnace
Usage
Sand Casting
Fuel
Gas
Manufacturing Level
B
1
2
3
4
Transport Package
Plywood
Specification
100*100*200
Trademark
semc
Origin
Shanghai China
HS Code
8501400000
Production Capacity
20set/Month
Packaging & Delivery
Package Size
900.00cm * 800.00cm * 700.00cm
Package Gross Weight
500.000kg
Product Description
We supply Electric Slag Remelting Furnace
Electric Slag Remelting Furnace
The ESR process involves the gradual melting of the lower end of a cast or forged electrode through a layer of molten metallurgically active slag into a water-cooled copper mold. The slag is usually calcium fluoride with the addition of lime, magnesia, alumina and other oxides. In its molten state the slag is electrically conductive and acts like a resistance heating element when a high current is passed between the electrode and the mold. With the continued passage of electric current the slag becomes superheated. The electrode tip is immersed in this superheated slag and begins to melt. The immersion of the electrode in the slag is precisely maintained and a controlled melt rate is established. An advanced computer control system maintains the melt rate and electrode immersion utilizing custom designed algorithms taking into account measurements from the load beam weighing system, measurements of the furnace voltage (or resistance), and measurements of voltage (or resistance) swing. The molten metal droplets sink through the lower density molten slag and re-solidify in the water-cooled copper mold. Through this process the slag-metal reactions dissolve inclusions and purify the metal as it falls through the molten slag. After the process has continued for some time, a purified ingot having a controlled solidification structure is built up in the mold. The slag floating on top of the liquid metal pool also acts to prevent oxidation of the molten metal when melting in air. It is also common for the ESR process to take place in an inert gas environment to further prevent oxidation of the metal and to prevent oxidation of the slag. Toward the end of the process, the power is gradually reduced providing a controlled hot top. The resulting ingot is structurally sound, chemically homogeneous, and provides a high yield of useful product.
Induction furnace is used for smelting or insulating ferrous metals, non-ferrous metals, sponge iron, such as scrap iron, scrap steel, copper, aluminum and so on. Complete working equipment such as continuous casting machine, rolling mill, mainly used for the production of billet, steel bar, angle steel, H-beam, I-beam, etc. Using KGPS, IGBT, single or double power supply technology, PLC (Siemens) can be realized throughout the monitoring.
Main supply list: 2 sets of electric furnace body, 2 sets of hydraulic or mechanical tilting electric furnace mechanism, 1 set of control platform, 1 set of intermediate frequency control cabinet (6 pulse 1, 12 pulse 2, 24 pulse 4), low voltage control cabinet (6 pulse 1, 12 pulse 2, 24 pulse 4), 1 set of capacitor cabinet, 4 or 8 water-cooled cables; 1 water temperature alarm, 1 leakage alarm; 1 crucible mold, 1 liquid One batch of pressure steel pipe, one set of copper row, three water tanks. Transformer, cooling tower, furnace builder, furnace lining ejector, furnace cover.
KGSP Induction Electric Furnace
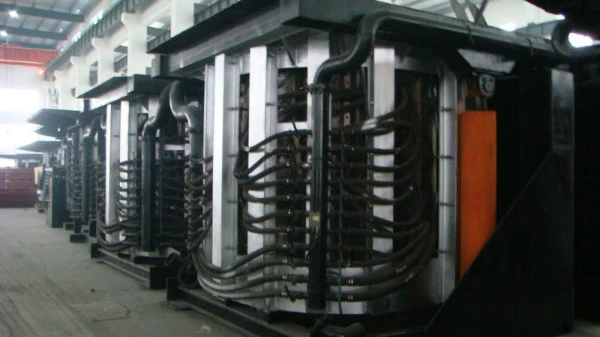
GW-8-4000-0.5J KGSP Induction Electric Furnace
GW-1-750-1JJ Medium frequency coreless electric furnace
GW-50-22000-0.2J No induction melting furnace
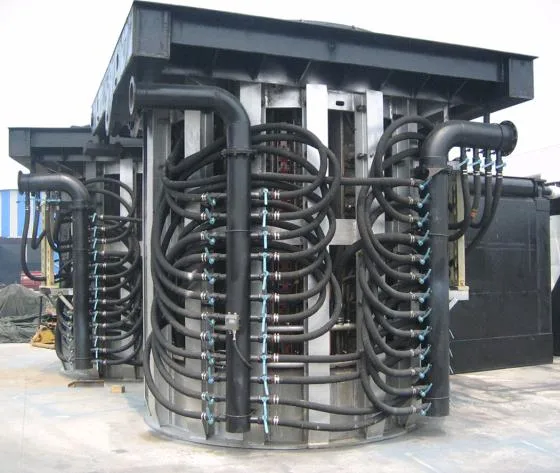
GW-0.25-160-1JJ melting electric furnace
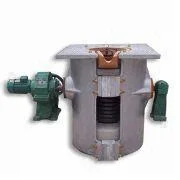
GW-1.5-1000-1J Medium frequency induction furnace
Note:
(1) GW - means medium frequency induction furnace, - 1 - means induction furnace capacity of 1 ton, - 500 - means furnace rated power of 500 KW, / 1 - means furnace operating frequency of 1000 Hz, / 0.5 - means melting furnace frequency of 500 Hz, - J - means hydraulic tilting furnace (furnace shell is steel shell), - JJ - means mechanical tilting furnace. (the shell of the furnace is aluminum alloy).
(2) The above quoted price is for routine configuration. Other configurations can be added, such as leak alarm, water temperature alarm, furnace switch, cover mechanism, lining ejector and transformer, cooling device (open and close cooling tower, closed cooling tower, plate heat exchanger)
3) If necessary, send technicians to carry out the commissioning: the domestic section is free; the overseas section travel expenses, accommodation and food are borne by the user and each person is subsidized 150 US dollars per day.
4) I quote EX-W at a price including simple packing, including shipping charges to Shanghai port area and all inland charges in China.
V) The above electric furnace voltage levels are 380V, 690V and 950/1000V, and the frequency is 50HZ. If the user equipment requirements are different from the above voltage levels and frequencies, each item needs to be increased by 15000USD.
Electric Slag Remelting Furnace
The ESR process involves the gradual melting of the lower end of a cast or forged electrode through a layer of molten metallurgically active slag into a water-cooled copper mold. The slag is usually calcium fluoride with the addition of lime, magnesia, alumina and other oxides. In its molten state the slag is electrically conductive and acts like a resistance heating element when a high current is passed between the electrode and the mold. With the continued passage of electric current the slag becomes superheated. The electrode tip is immersed in this superheated slag and begins to melt. The immersion of the electrode in the slag is precisely maintained and a controlled melt rate is established. An advanced computer control system maintains the melt rate and electrode immersion utilizing custom designed algorithms taking into account measurements from the load beam weighing system, measurements of the furnace voltage (or resistance), and measurements of voltage (or resistance) swing. The molten metal droplets sink through the lower density molten slag and re-solidify in the water-cooled copper mold. Through this process the slag-metal reactions dissolve inclusions and purify the metal as it falls through the molten slag. After the process has continued for some time, a purified ingot having a controlled solidification structure is built up in the mold. The slag floating on top of the liquid metal pool also acts to prevent oxidation of the molten metal when melting in air. It is also common for the ESR process to take place in an inert gas environment to further prevent oxidation of the metal and to prevent oxidation of the slag. Toward the end of the process, the power is gradually reduced providing a controlled hot top. The resulting ingot is structurally sound, chemically homogeneous, and provides a high yield of useful product.
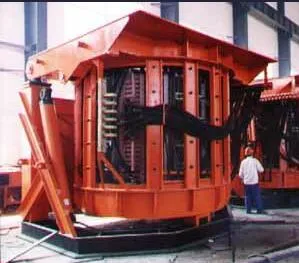
Induction furnace is used for smelting or insulating ferrous metals, non-ferrous metals, sponge iron, such as scrap iron, scrap steel, copper, aluminum and so on. Complete working equipment such as continuous casting machine, rolling mill, mainly used for the production of billet, steel bar, angle steel, H-beam, I-beam, etc. Using KGPS, IGBT, single or double power supply technology, PLC (Siemens) can be realized throughout the monitoring.
Main supply list: 2 sets of electric furnace body, 2 sets of hydraulic or mechanical tilting electric furnace mechanism, 1 set of control platform, 1 set of intermediate frequency control cabinet (6 pulse 1, 12 pulse 2, 24 pulse 4), low voltage control cabinet (6 pulse 1, 12 pulse 2, 24 pulse 4), 1 set of capacitor cabinet, 4 or 8 water-cooled cables; 1 water temperature alarm, 1 leakage alarm; 1 crucible mold, 1 liquid One batch of pressure steel pipe, one set of copper row, three water tanks. Transformer, cooling tower, furnace builder, furnace lining ejector, furnace cover.
KGSP Induction Electric Furnace
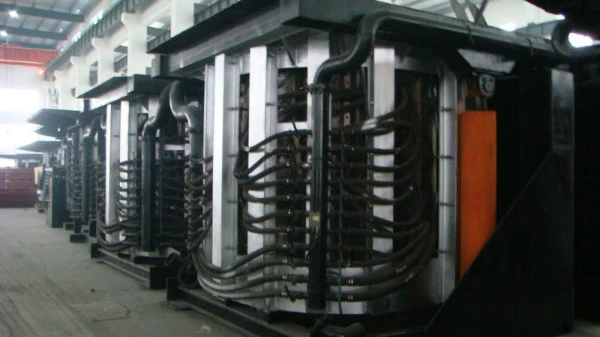
GW-8-4000-0.5J KGSP Induction Electric Furnace
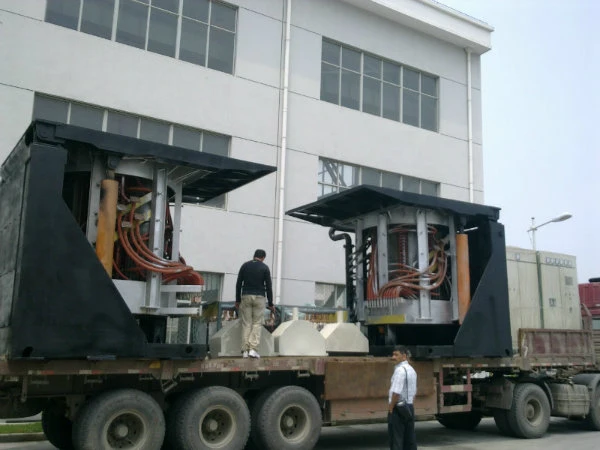
GW-1-750-1JJ Medium frequency coreless electric furnace
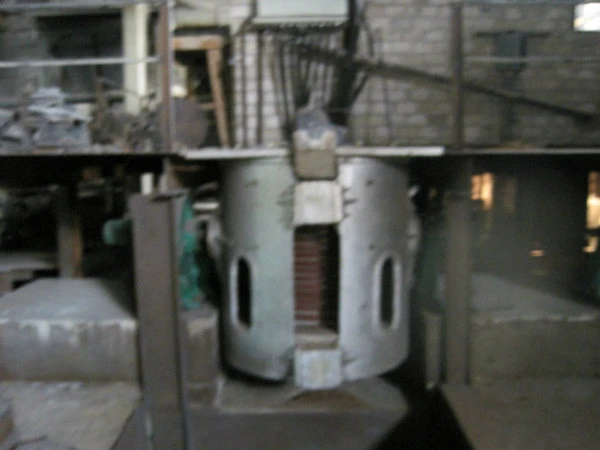
GW-50-22000-0.2J No induction melting furnace
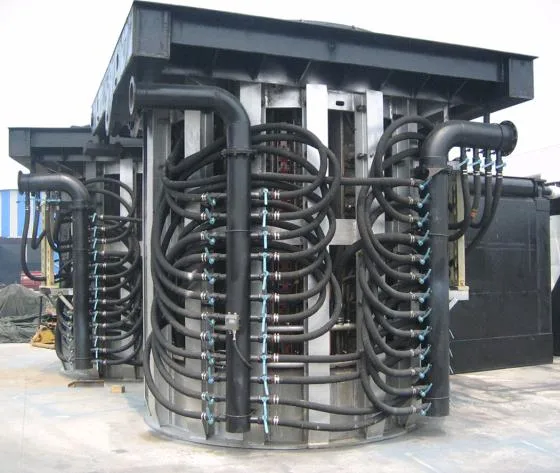
GW-0.25-160-1JJ melting electric furnace
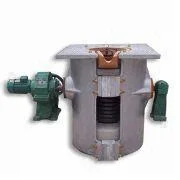
GW-1.5-1000-1J Medium frequency induction furnace
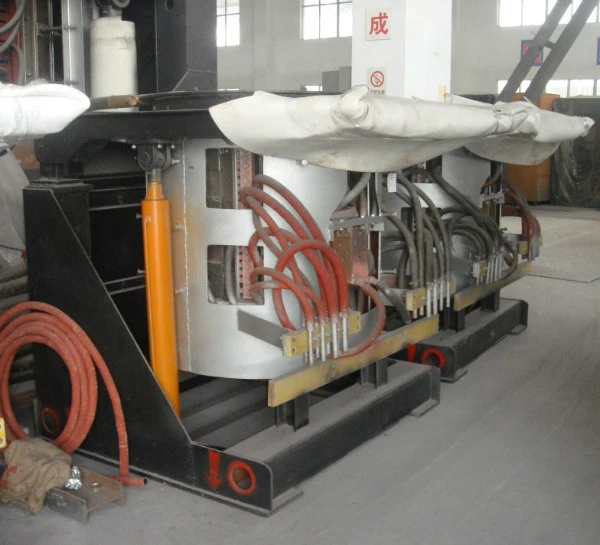
NO. | Electric Furnace Type | Input power (KW) | input voltage (V) | Input current (A) | Rated power (KW) | DC current (A) | DC voltage (V) | Melting rate (T/H) | working frequency (HZ) | working voltage (V) | cooling water pressure(MPA) | Rated capacity (T) | Power consumption (KWH/T) | |
Power Supply | Furnace body | |||||||||||||
1 | GW-0.25-160/1JJ | 180 | 380 (6 Pulse) | 256 | 160 | 320 | 500 | 0.24 | 1000 | 750 | 0.1~0.15 | 0.25~0.3 | 0.25 | 790 |
2 | GW-0.5-250/1JJ | 280 | 380 (6 Pulse) | 400 | 250 | 500 | 500 | 0.4 | 1000 | 1500 | 0.1~0.15 | 0.25~0.3 | 0.5 | 770 |
3 | GW-0.5-250/1J | 280 | 380 (6 Pulse) | 400 | 250 | 500 | 500 | 0.4 | 1000 | 1500 | 0.1~0.15 | 0.25~0.3 | 0.5 | 770 |
4 | GW-0.75-400/1JJ | 400 | 380 (6 Pulse) | 650 | 400 | 800 | 500 | 0.6 | 1000 | 1500 | 0.1~0.15 | 0.25~0.3 | 0.75 | 770 |
5 | GW-0.75-400/1J | 400 | 380 (6 Pulse) | 650 | 400 | 800 | 500 | 0.6 | 1000 | 1500 | 0.1~0.15 | 0.25~0.3 | 0.75 | 770 |
6 | GW-1-500/1JJ | 550 | 380 (6 Pulse) | 800 | 500 | 1000 | 500 | 0.8 | 1000 | 1500 | 0.1~0.15 | 0.25~0.3 | 1 | 750 |
7 | GW-1-750/1JJ | 800 | 380/690 (6 Pulse) | 1200/ 700 | 750 | 1500/ 850 | 500/ 880 | 0.9 | 1000/ 500 | 1500/ 2600 | 0.1~0.15 | 0.25~0.3 | 1 | 720/660 |
8 | GW-1-750/1J | 800 | 380/690 (6 Pulse) | 1200/ 700 | 750 | 1500/ 850 | 500/ 880 | 0.9 | 1000/ 500 | 1500/ 2600 | 0.1~0.15 | 0.25~0.3 | 1 | 720/660 |
9 | GW-1.5-1000/0.5JJ | 1100 | 690 (6 Pulse) | 912 | 1000 | 1140 | 880 | 1.2 | 500 | 2600 | 0.1~0.15 | 0.25~0.3 | 1.5 | 700 |
10 | GW-1.5-1000/0.5J | 1100 | 690 (6 Pulse) | 912 | 1000 | 1140 | 880 | 1.2 | 500 | 2600 | 0.1~0.15 | 0.25~0.3 | 1.5 | 700 |
11 | GW-2-1500/0.5JJ | 1650 | 690 (6 Pulse) | 1360 | 1500 | 1700 | 880 | 1.7 | 500 | 2600 | 0.1~0.15 | 0.25~0.3 | 2 | 675 |
12 | GW-2-1500/0.5J | 1650 | 690 (6 Pulse) | 1360 | 1500 | 1700 | 880 | 1.7 | 500 | 2600 | 0.1~0.15 | 0.25~0.3 | 2 | 675 |
13 | GW-2-2000/0.5JJ | 2200 | 690 (6 Pulse) | 1400 | 2000 | 2275 | 880 | 1.9 | 500 | 2600 | 0.1~0.15 | 0.25~0.3 | 2 | 650 |
14 | GW-3-2500/0.5JJ | 2750 | 690/950 (6 Pulse) | 2275/ 1700 | 2500 | 2840/ 2080 | 880/ 1250 | 2.56 | 500 | 2600/3200 | 0.1~0.15 | 0.25~0.3 | 3 | 610/560 |
15 | GW-3-2500/0.5J | 2750 | 690/950 (6 Pulse) | 2275/ 1700 | 2500 | 2840/ 2080 | 880/ 1250 | 2.56 | 500 | 2600/3200 | 0.1~0.15 | 0.25~0.3 | 3 | 610/560 |
16 | GW-4-3000/0.5J | 3300 | 690/950 (6 Pulse) | 2730/ 2040 | 3000 | 3410/ 2500 | 880/ 1250 | 3.2 | 500 | 2600/3200 | 0.1~0.15 | 0.25~0.3 | 4 | 610/560 |
17 | GW-5-4000/0.5J | 4400 | 950 (6 Pulse) | 2300 | 4000 | 3330 | 1250 | 5 | 500 | 3400 | 0.1~0.15 | 0.25~0.3 | 5 | 600/550 |
18 | GW-6-4000/0.5J | 4400 | 950 (12 Pulse) | 2300 | 4000 | 3330 | 1250 | 5 | 500 | 3400 | 0.1~0.15 | 0.25~0.3 | 6 | 600/550 |
19 | GW-8-5000/0.5J | 5000 | 950 (12 Pulse) | 3400 | 5000 | 4200 | 1250 | 7~8 | 500 | 3400 | 0.1~0.15 | 0.25~0.3 | 8 | 600/550 |
20 | GW-10-6000/0.5J | 6300 | 950 (12 Pulse) | 3750 | 6000 | 4600 | 1250 | 8.5~9 | 500 | 3400 | 0.1~0.15 | 0.25~0.3 | 10 | 600/550 |
21 | GW-12-8000/0.25J | 8000 | 950 (12 Pulse) | 4900 | 8000 | 6000 | 1250 | 9~10.5 | 250 | 3400 | 0.1~0.15 | 0.25~0.3 | 12 | 600-550 |
22 | GW-15-8000/0.25J | 8000 | 950 (12 Pulse) | 4900 | 8000 | 6000 | 1250 | 9~10.5 | 250 | 3400 | 0.1~0.15 | 0.25~0.3 | 15 | 600-550 |
23 | GW-15-10000/0.25J | 10000 | 950 (24 Pulse) | 6500 | 10000 | 8000 | 1250 | 13~15 | 250 | 3400 | 0.1~0.15 | 0.25~0.3 | 15 | 600-550 |
24 | GW-18-12000/0.25J | 12000 | 950 (24 Pulse) | 8160 | 12000 | 10000 | 1200 | 15~17 | 250 | 3400 | 0.1~0.15 | 0.25~0.3 | 18 | 600-550 |
25 | GW-20-12000/0.25J | 12000 | 950 (24 Pulse) | 8160 | 12000 | 10000 | 1200 | 17~19 | 250 | 3400 | 0.1~0.15 | 0.25~0.3 | 20 | 600-550 |
26 | GW-25-14000/0.25J | 14000 | 950 (24 Pulse) | 9460 | 14000 | 11600 | 1200 | 19~21 | 150~200 | 3400 | 0.1~0.15 | 0.25~0.3 | 25 | 600-550 |
27 | GW-30-16000/0.2J | 16000 | 950 (24 Pulse) | 10850 | 16000 | 13300 | 1200 | 21~23 | 150~200 | 3400 | 0.1~0.15 | 0.25~0.3 | 30 | 600-550 |
28 | GW-40-20000/0.2J | 20000 | 950 (24 Pulse) | 13545 | 20000 | 16600 | 1200 | 25~27 | 150~200 | 3400 | 0.1~0.15 | 0.25~0.3 | 40 | 600-550 |
29 | GW-50-22000/0.2J | 22000 | 950 (24 Pulse) | 14932 | 22000 | 18300 | 1200 | 25~28 | 150~200 | 3400 | 0.1~0.15 | 0.25~0.3 | 50 | 600-550 |
Note:
(1) GW - means medium frequency induction furnace, - 1 - means induction furnace capacity of 1 ton, - 500 - means furnace rated power of 500 KW, / 1 - means furnace operating frequency of 1000 Hz, / 0.5 - means melting furnace frequency of 500 Hz, - J - means hydraulic tilting furnace (furnace shell is steel shell), - JJ - means mechanical tilting furnace. (the shell of the furnace is aluminum alloy).
(2) The above quoted price is for routine configuration. Other configurations can be added, such as leak alarm, water temperature alarm, furnace switch, cover mechanism, lining ejector and transformer, cooling device (open and close cooling tower, closed cooling tower, plate heat exchanger)
3) If necessary, send technicians to carry out the commissioning: the domestic section is free; the overseas section travel expenses, accommodation and food are borne by the user and each person is subsidized 150 US dollars per day.
4) I quote EX-W at a price including simple packing, including shipping charges to Shanghai port area and all inland charges in China.
V) The above electric furnace voltage levels are 380V, 690V and 950/1000V, and the frequency is 50HZ. If the user equipment requirements are different from the above voltage levels and frequencies, each item needs to be increased by 15000USD.