Basic Info.
Product Description
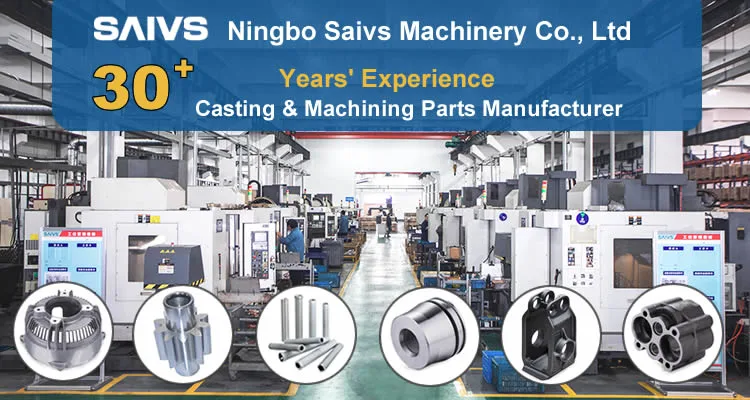
Products Description
What is Sand Casting
Sand casting, known as sand molding casting, is a casting process that uses sand as a mold. Then pour the liquid metal into this mold to create a casting part.It is one of the oldest casting processes. It can be used to make metal components of all sizes, ranging from 1kg to hundred tons. The statistics show more than 61% of all metal castings are produced by sand casting.
In modern industry, the sand casting Process controls, material options, tolerance capabilities, the ability to produce elaborate parts, broad size ranges have all come a very long way. It has several unique advantages.
The advantages of sand casting
- Suitable for more metals types.
- Can be for large size, Complex shapes sand casting products
- Compare with other metal forming processes, Tooling and equipment cost is low
- Scrap metal can be recycled
- Short lead time
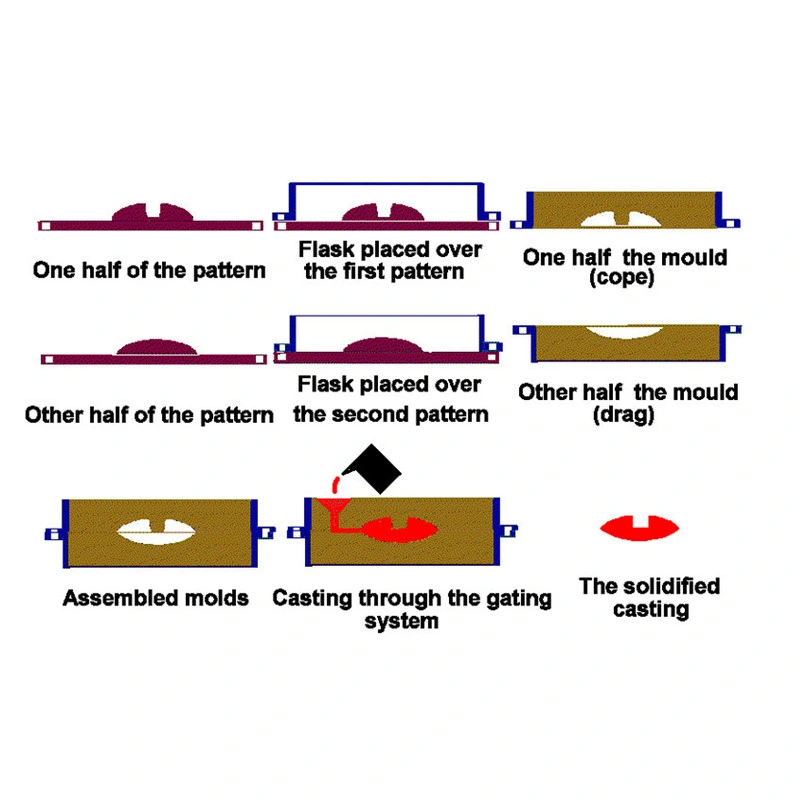
Applications of sand casting
It is difficult to grasp how many different technologies use sand casting. Its versatility as a casting process makes it ideal for almost any complex part, and almost every modern technology benefits from this manufacturing process. Below is a list of only a few of the products which are fabricated using the sand casting process, which shows just how varied the possible applications can be.
Sand casting is used to create such products as:
- Many kinds of pistons and valves
- Blowers/impellers
- Cams, bushing, and bearings
- Electronic equipment
- Gas/oil tanks
- Most hardware
- Engine blocks
- Automobile parts
- Screws, nuts, and gears
- Agricultural machines
- Medical equipment
- Mining equipment
and much more.
Sand Casting Materials
Sand Casting, or sand metal casting, is a process using sand as the molding material to produce metal castings. The term is also used to refer to the products produced by this process. Metals cast using the process include tin, cast iron, aluminum and steel, as well as copper and bronze. Sand casting is used to produce over seventy percent of all metal castings, some of these include metal tools, car parts and plumbing. These castings are produced in specialized foundries and factories, and the process is considered an economical option because it requires less technology and cost.
Material | Aluminum: AL6061, Al6063, AL6082, AL7075, AL5052, AL2024 |
Stainless steel: SS201, SS301, SS303, SS304, SS316, SS430 etc | |
Steel: mild steel/ carbon steel including 1010, 1020, 1045, 1050, Q690 etc | |
Brass: HPb63, HPb62, HPb61, HPb59, H59, H68, H80, H90 etc. | |
Copper: C11000, C12000, C12000, C17200, C72900, C36000 etc. | |
Processing Equipment | Germany brand Laser cutter, CNC shearing machine, CNC bending machine, |
(CNC) stamping machine, Hyraulic Machine, Various welding machine, CNC machine center. | |
Surface Treatment | Aluminum: Anodization, Sandblast, Brushing, Polishing, Electro-plating etc |
Stainless Steel: Polishing, Brushing, Passivating, Sandblasting, Electro-plating | |
Steel: Zinc plating, Nickel plating, Chrome plating, Powder Coating, Painting etc | |
Brass & Copper: Brushing, Polishing etc | |
Precision | + - 0.1mm |
Application | Railway, Auto, Truck, Medical, Machinery, Equipment, Electronic, Electrical etc |
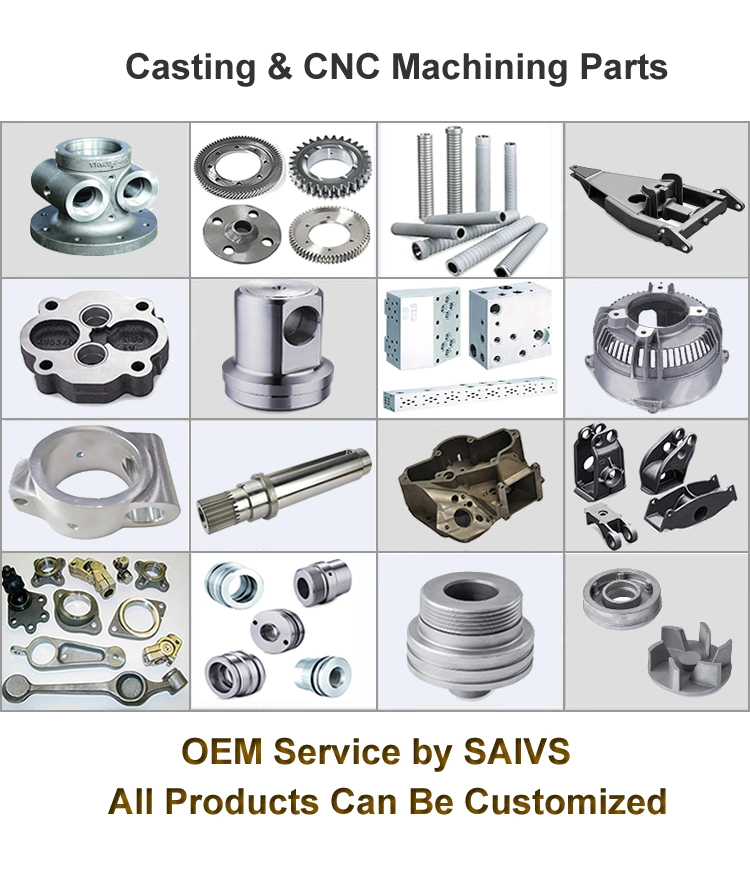
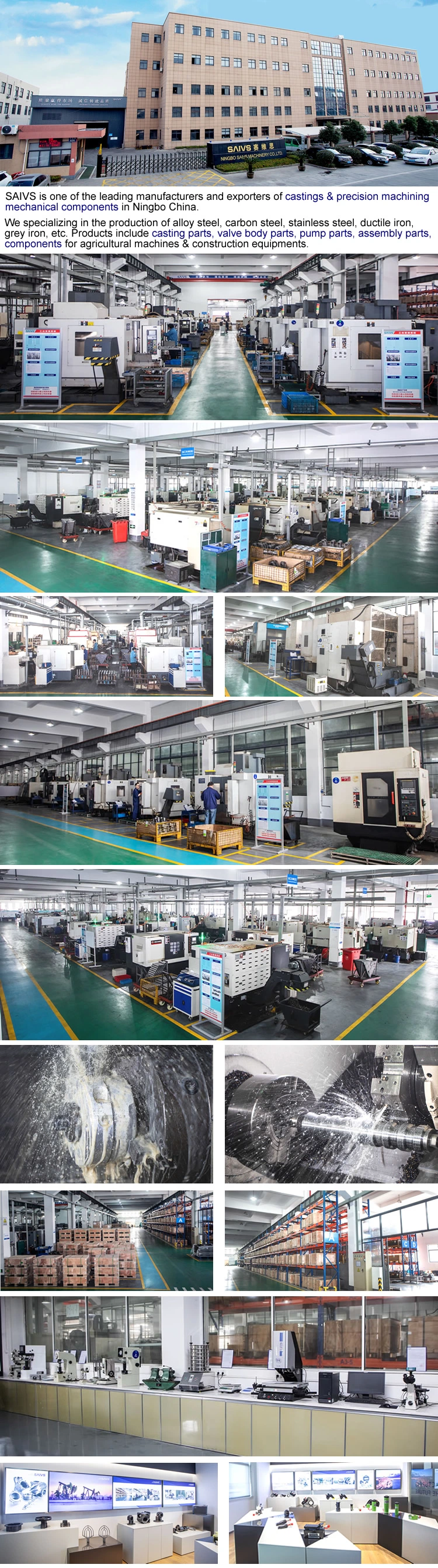
FAQ
Q: Are you a trading company or manufacturer?
A: We are a factory with more than 20 years' experience.
Q: How long for delivery?
A: Generally it is 15-30days as we are a customized service we confirm with customers when place order.
Q: What is the MOQ?
A: It depends on what you are buying. Normally, our minimum order is one 20' full container and an LCL container (less than a
container load) can be acceptable.
Q: Can you customize my products?
A: Yes, we can customize products with your design drawings like DWG, DXF, DXW, IGES, STEP, PDF, etc.
Q: What is your terms of payment?
A: 30% T/T in advance, balance before shipment, or as per discussion.
Q: What about your quality control?
A: * . Checking the raw material after they reach our factory-----Incoming quality control(IQC)
* . Checking the details before the production line operated
* . Have a full inspection and routing inspection during mass production----In-process quality control(IPQC)
* . Checking the goods after they are finished----Final quality control(FQC)
* . Checking the goods after they are finished----Outgoing quality control(QC) * . 100% inspection and delivery before shipment