- Overview
- Company Profile
- Certifications
- Packaging & Shipping
- FAQ
Basic Info.
Dimensions
Customized Sizes
Transport Package
Non Fumigation Wooden Box
Specification
0.25T/0.5T/1T/2T/3T/5T
Trademark
SC
Origin
China
Production Capacity
500000 Pieces/Year
Product Description
Material | HT150-HT300 Gray iron,QT400-18 /QT900-2 Ductile Iron(Aupon your requirements) |
Application | Auto, Building, Capital equipment, Energy, Instrumentation, Medical device etc |
Technics | casting |
Tooling Design | We have own R&D team to make customized tooling, usually 7-15 days can be ready. |
Standard | China GB high precision standard. |
Surface Finish | 200ºC(392ºF) |
Surface Treatment | Mill Finishing, Anodizing, Powder coating etc(Aupon your requirements) |
Drawing | 3D Drawing: .step / .stp, 2D Drawing: .dxf/ .dwg / .pdf |
Color | Customized |
Delivery time | According to the quantities and specifications of each order. Normal delivery times are from 30 to 45 days after receiving the deposit. |
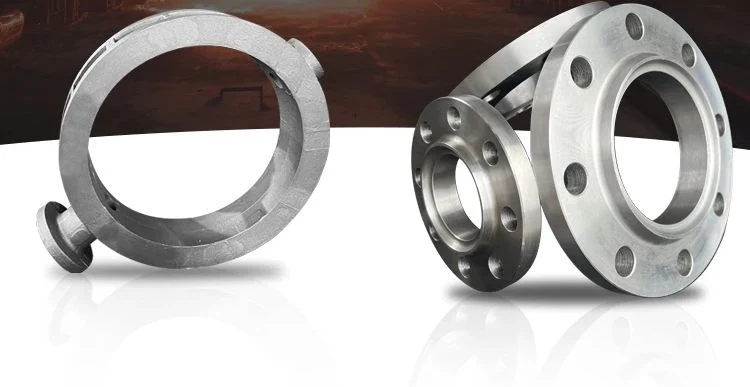
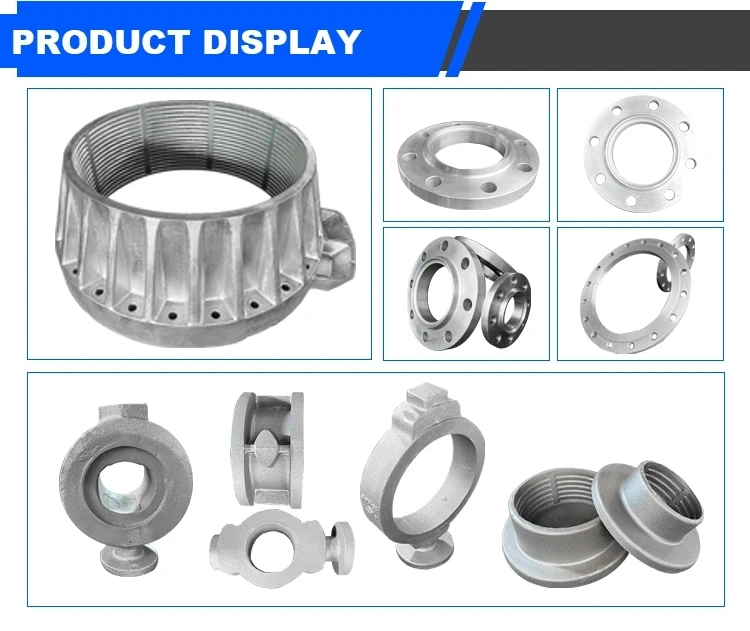
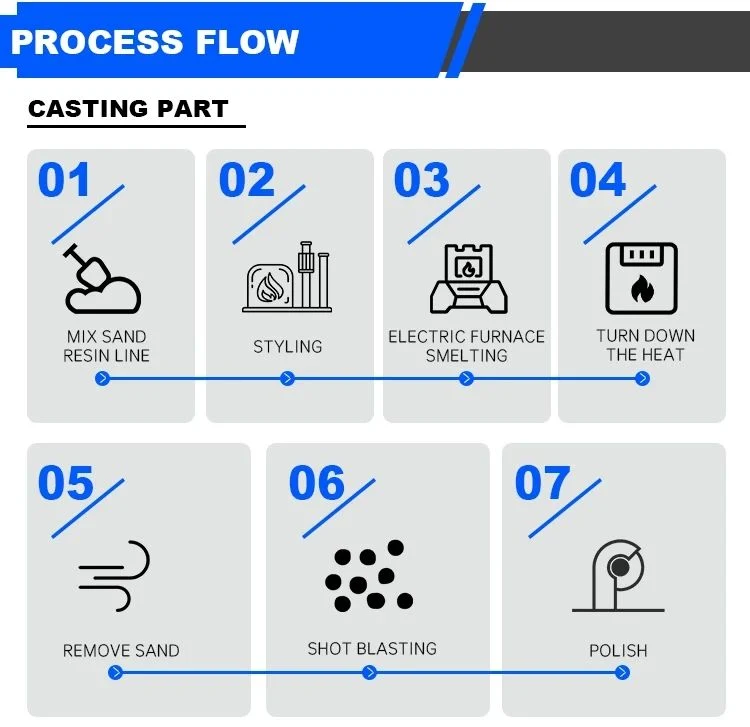
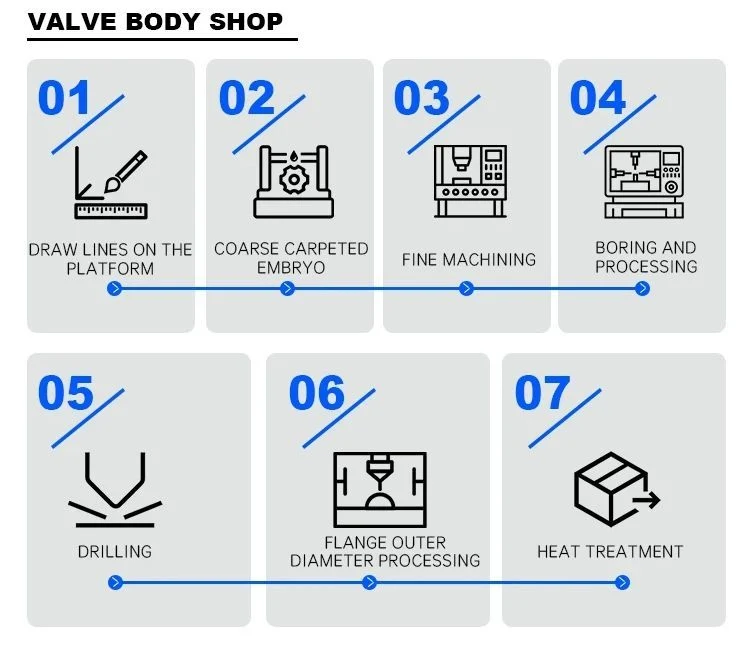
The ring forging process is a process that utilizes metal materials for forging processing. It mainly obtains the required shape and performance through heat treatment and forging processing of metal materials. The ring forging process usually includes the following main steps: raw material preparation, forging forming, heat treatment, and subsequent processing.
Firstly, raw materials need to be screened and cut to ensure their quality and dimensions meet the requirements. Then, the raw materials are placed in a heating furnace for heating treatment to reach the appropriate forging temperature. The temperature and time of heating treatment need to be controlled according to the characteristics and requirements of the metal material to ensure the quality and performance of the forging.
After the heating treatment is completed, the metal material can be forged using die forging to obtain more complex and accurate shapes. During the forging process, it is necessary to control parameters such as forging temperature, forging speed, and forging force to ensure the quality and dimensional accuracy of the forgings.
After forging, the forging needs to undergo heat treatment to enhance its structure and performance. The heat treatment process involves cooling the forging through media such as water and oil. During the cooling process, it is necessary to control the cooling speed and temperature to avoid problems such as cracks and deformation in the forging.
The forging still needs to undergo subsequent processing to achieve the final shape and size requirements. Subsequent processing can include processes such as trimming and surface treatment. Trimming is the process of cutting and removing excess material from a forging to make its shape more precise. Surface treatment can include sandblasting, plating, and other methods to enhance the corrosion resistance and aesthetics of forgings.
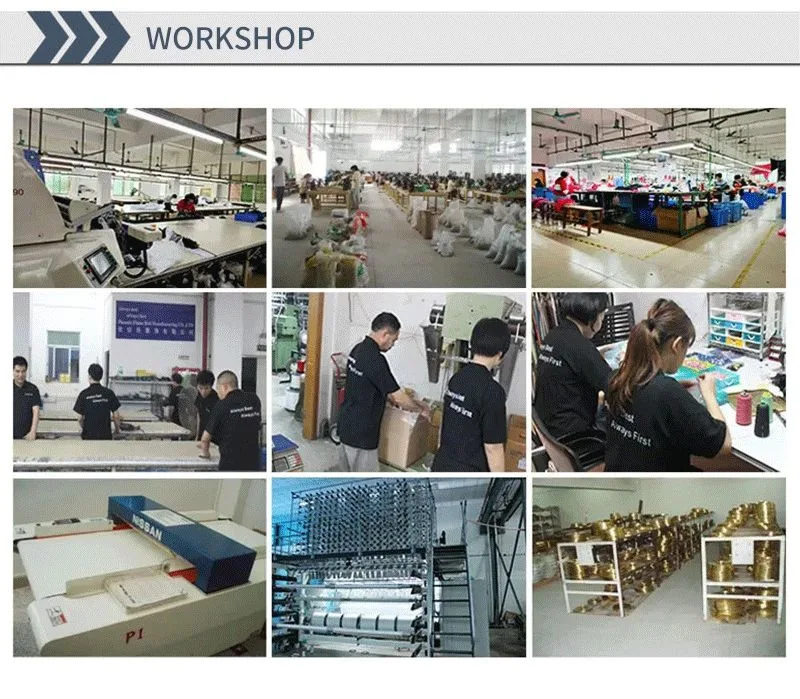
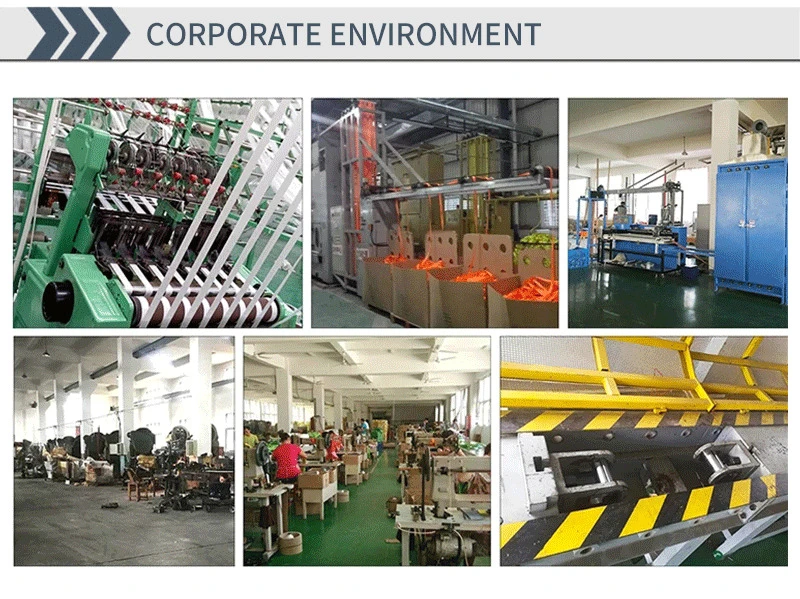
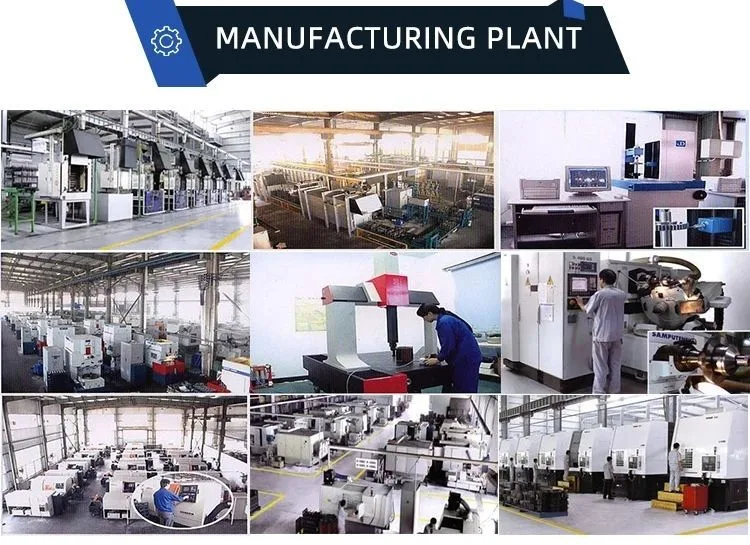
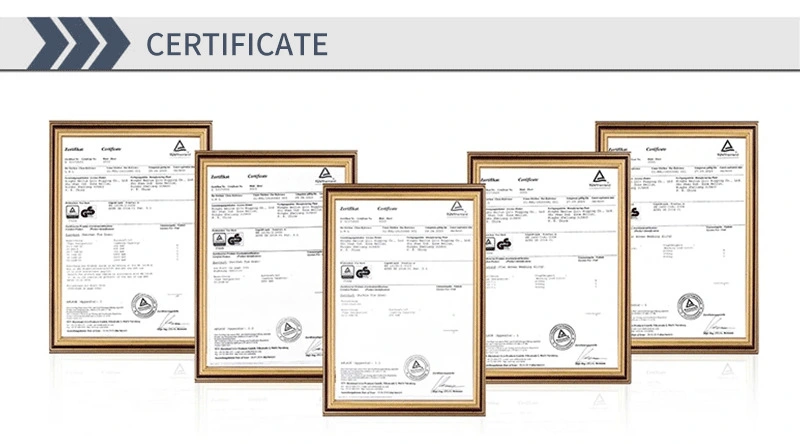
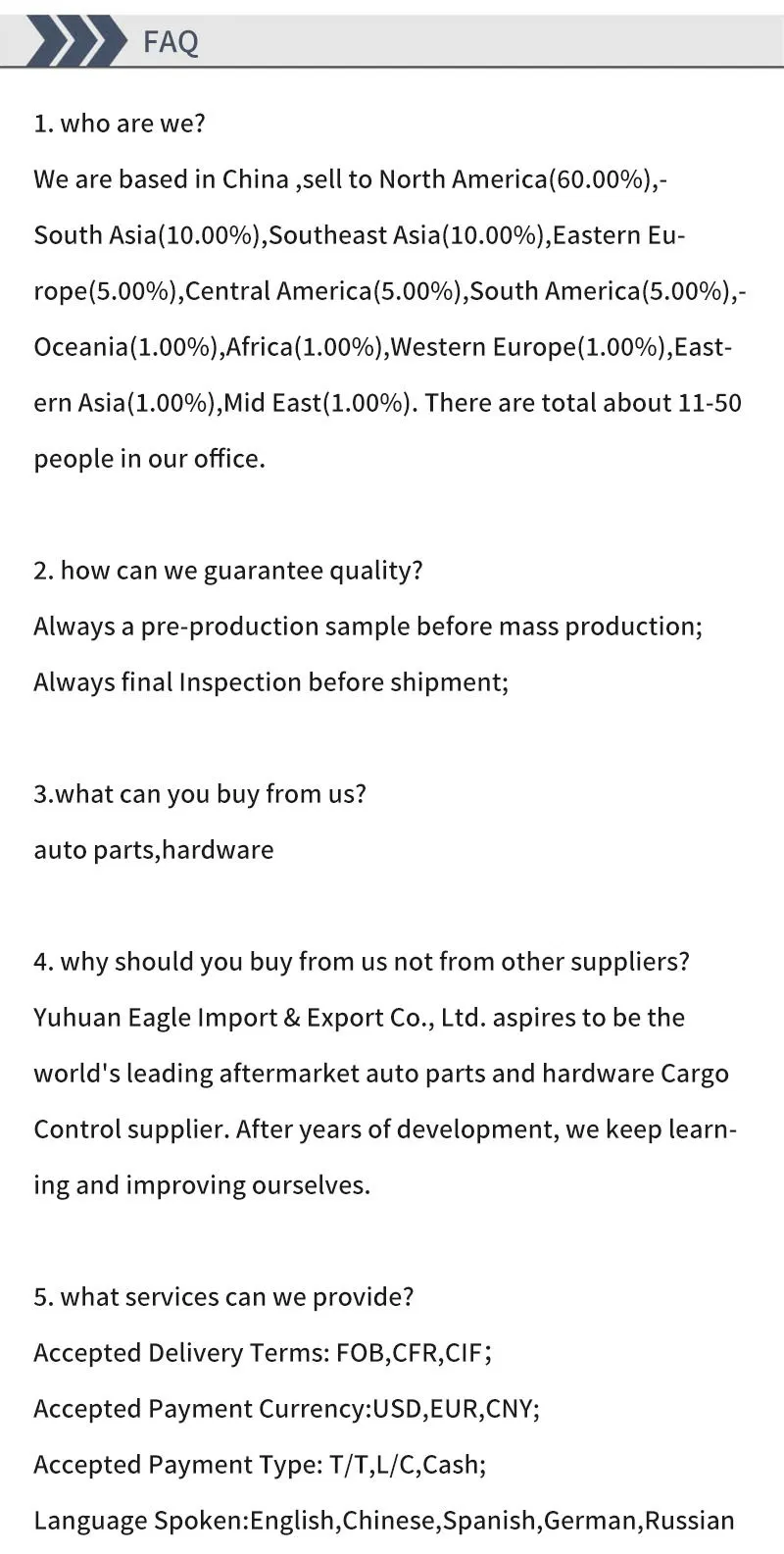