- Overview
- Company Profile
- Factory Facilities
Basic Info.
Packaging & Delivery
Product Description
A BRIEF INTRODUCTION OF THE CASTING BRANCH FACTORY:
COVERING AREA: | 45000m2 | |
PRODUCTION CAPACITY: | 20000ton/year for steel castings 3000ton/year for aluminum castings | |
PRODUCTION LINE: | VRH molding production line: 1 line Resin sand molding productino line: 1 line | |
WEIGHT OF UNIT PIECE: | from 20kg/pc to 10000kg/pc | |
CASTING TECHNOLOGY: | Computer Analog software system: PROE;KMCAD;KMCPP and so on | |
SMELTING EQUIPMENT | Electric-arc furnace: 5ton 2sets intermediate frequency smelting furnace:3ton 2sets LF refining furnace: 20ton 1set 250KG Experimental furnace | |
EQUIPMENT FOR HEATING PROCESSING: | Full-Automation trolley type resistance furnace Full-Autmation trolley type gas furnace | |
CERTIFICATES: | ISO9001; ISO14001; ISO18000 |
Our steel casting foundry is the largest in scale and earliest established national backbone enterprise in China's coal mining machinery industry and is affiliated to China National Coal Group Co., Ltd.
The casting branch, which is the main manufacturer of the China Coal Mining Machinery Limited Company, covering about 45000 square meters, is in the leading position in the domestic coal mining machinery casting market. We can produce carbon casting and alloy casting which is 20 kilograms to 10000 kilograms. The annual output of the casting branch is 20,000 tons of casting steel and 3,000 tons of casting aluminum parts. We now have 352 staff including 16 engineering technicians, 4 senior engineers, 35 technicians, 6 senior technicians, and 72 senior workers. Excellent technician personnel make a solid basis for high-quality casting. We enjoy a great reputation in the area of nationally owned coal mines, and always export our products to more than 10 countries like America, Britain, Vietnam, Bangladesh, Australia, and Turkey.
We have two production lines, one is the VRH molding production line, and another is the resin sand production line. It is more quick, accurate, and comprehensive for us to apply a computer simulation software system to the simulation of the casting process. Our main smelting equipment is electric arc furnaces, intermediate frequency furnaces, and L refining furnaces. And main heat equipment are trolley heat treatment furnaces, gas heat treatment furnaces, and auto-programming control systems. Our branch also has low-pressure casting equipment, by which we could produce high-quality alloy aluminum silicon parts which should be below 350 kilograms. With the help of the R&D capability of new materials and processes, a full set of lost foam casting equipment, and a 250-kilogram trail casting furnace, we can realize all kinds of casting tests for mass production.
The casting branch obtains advanced inspection and testing equipment, such as a vacuum direct reading spectrum analyzer,3D inspector, large-scale wet magnetic powder flaw detector, and dye penetrant inspection tester. Depending on the sand lab with complete function, and sophisticated testing method from the company testing center, we could manage each link, which are raw materials, production process, and final products.
Driven by the concept of green and clean production, the casting branch established a high-quality,high-efficiency, low-cost, clean, flexible, and agile casting system, we seek ways to secure workers' health, reduce pollution by advanced frequency dust cleaning system and adopting recycling and reusing casting materials and casting technique. As a green casting demonstration company acknowledged by the China Foundry Association, the casting branch is ready to build a "first-class green environmental casting company".
A BIRD'S-EYE VIEW OF THE ENTIRE FACTORY:
THE HOME OF THE CASTING PEOPLE-CASTING BRANCH:
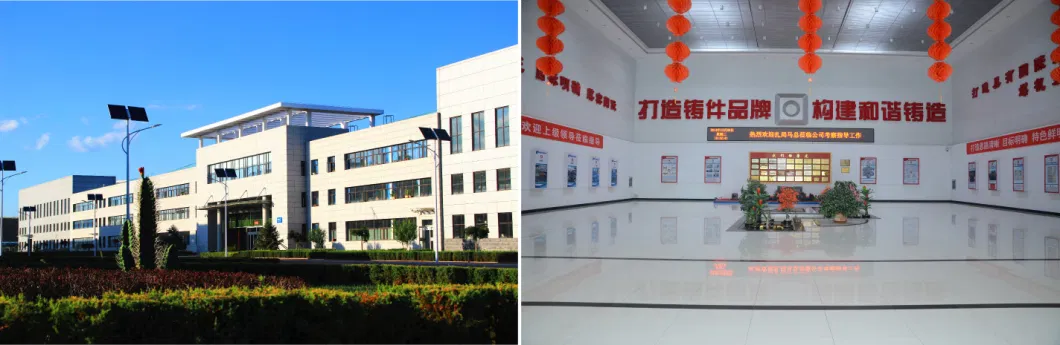
THE MAIN EQUIPMENT OF THE CASTING FACTORY:
♣Smelting Furnace: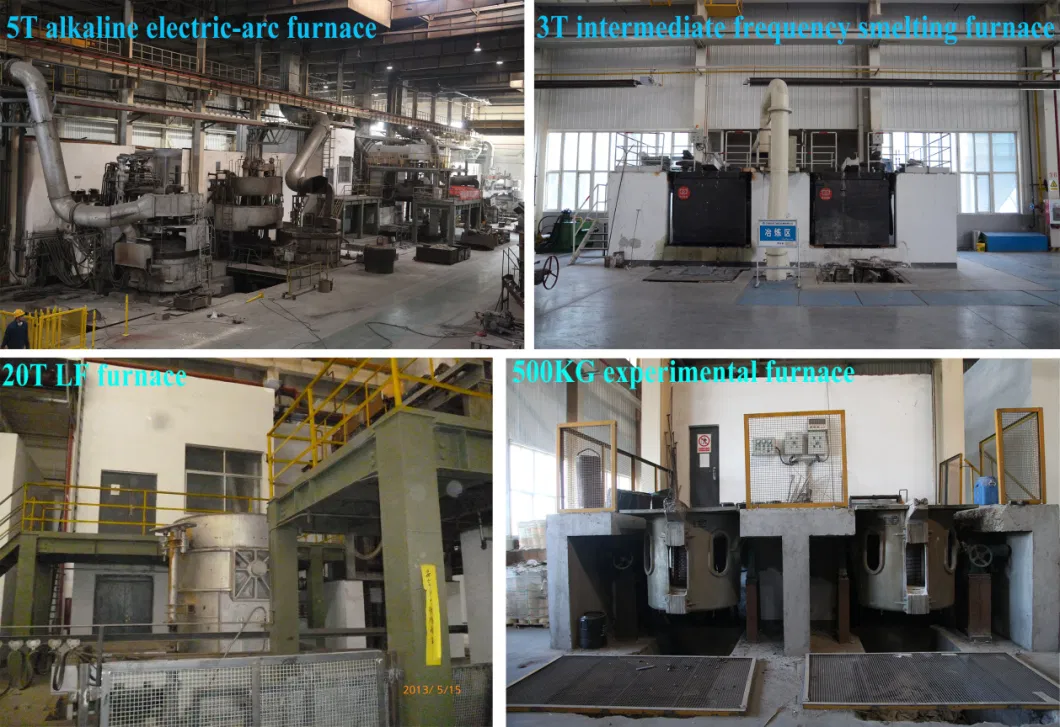
♣Processing Design:
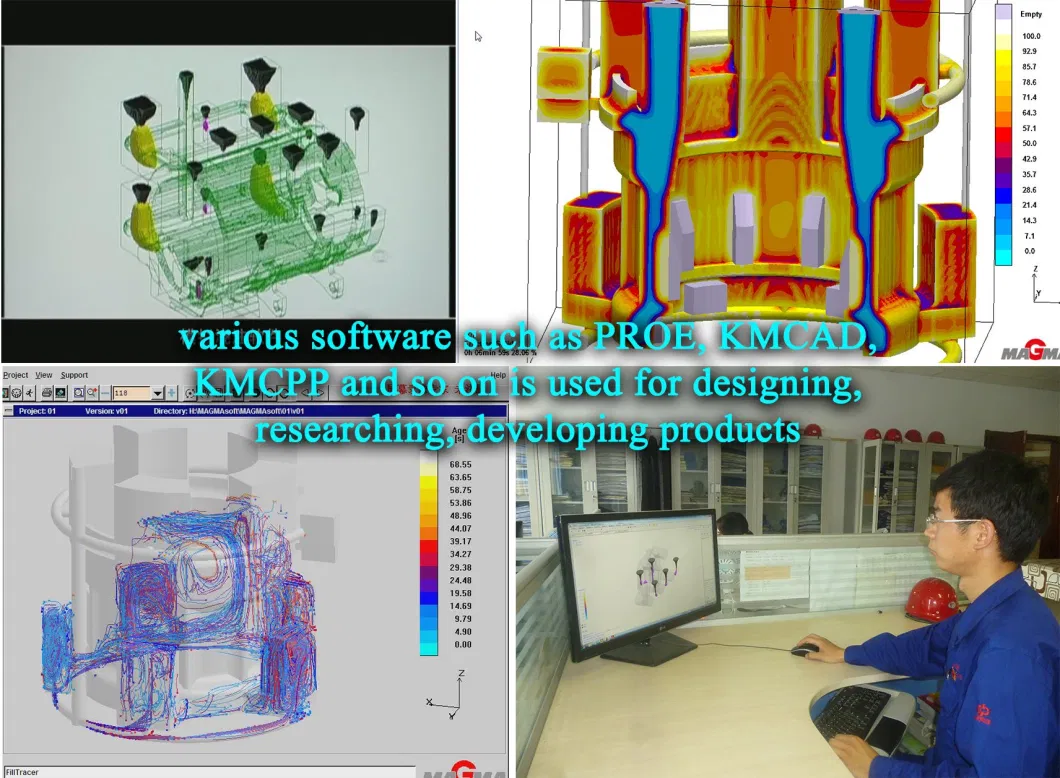
♣Molding Production Line:
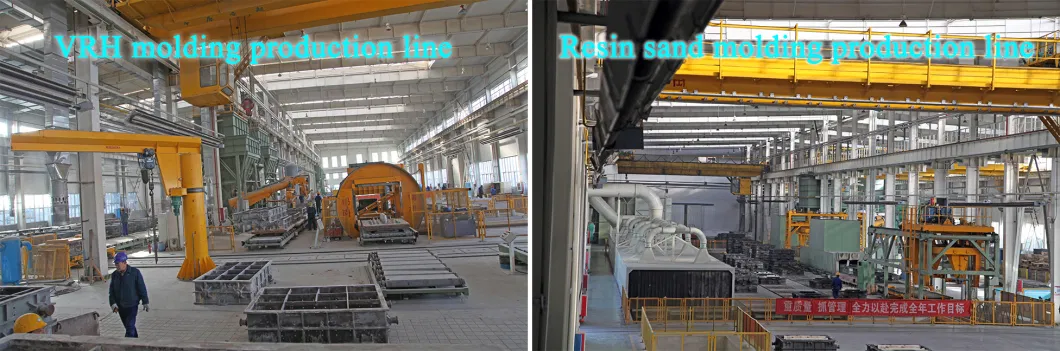
♣Heat-treating Equipment:
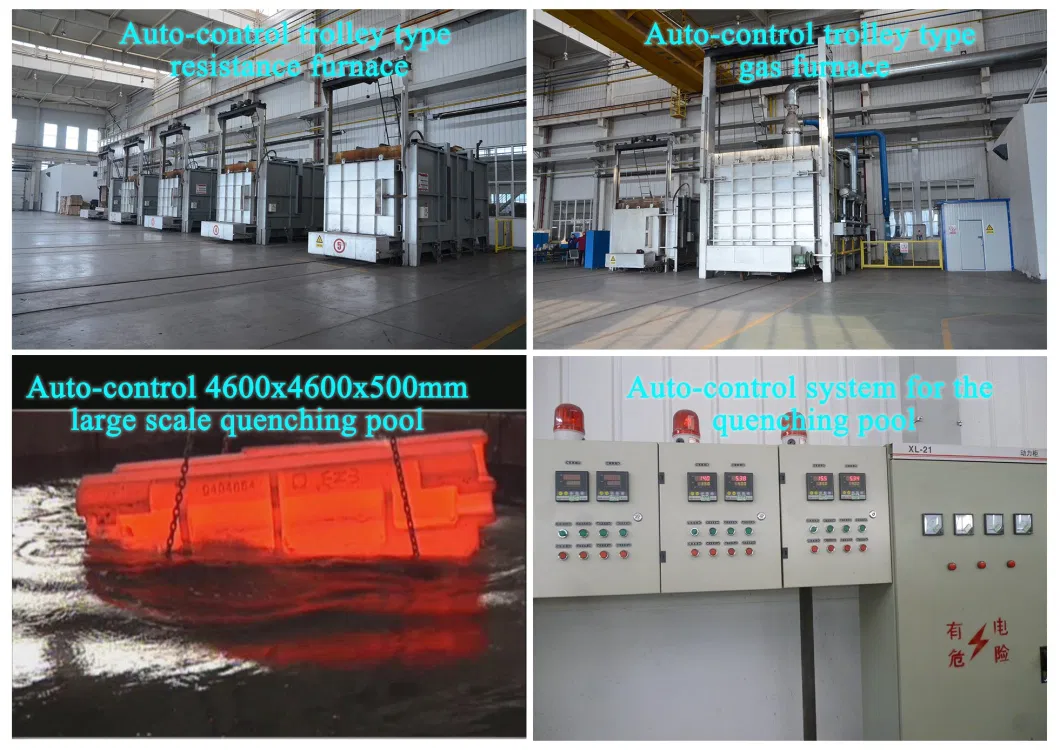
♣Cleaning Equipments and Workshops for Castings:
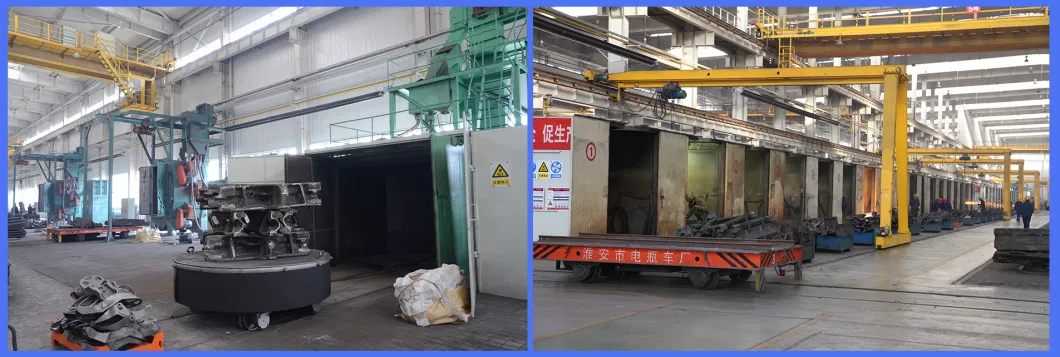
♣Dedusting System:
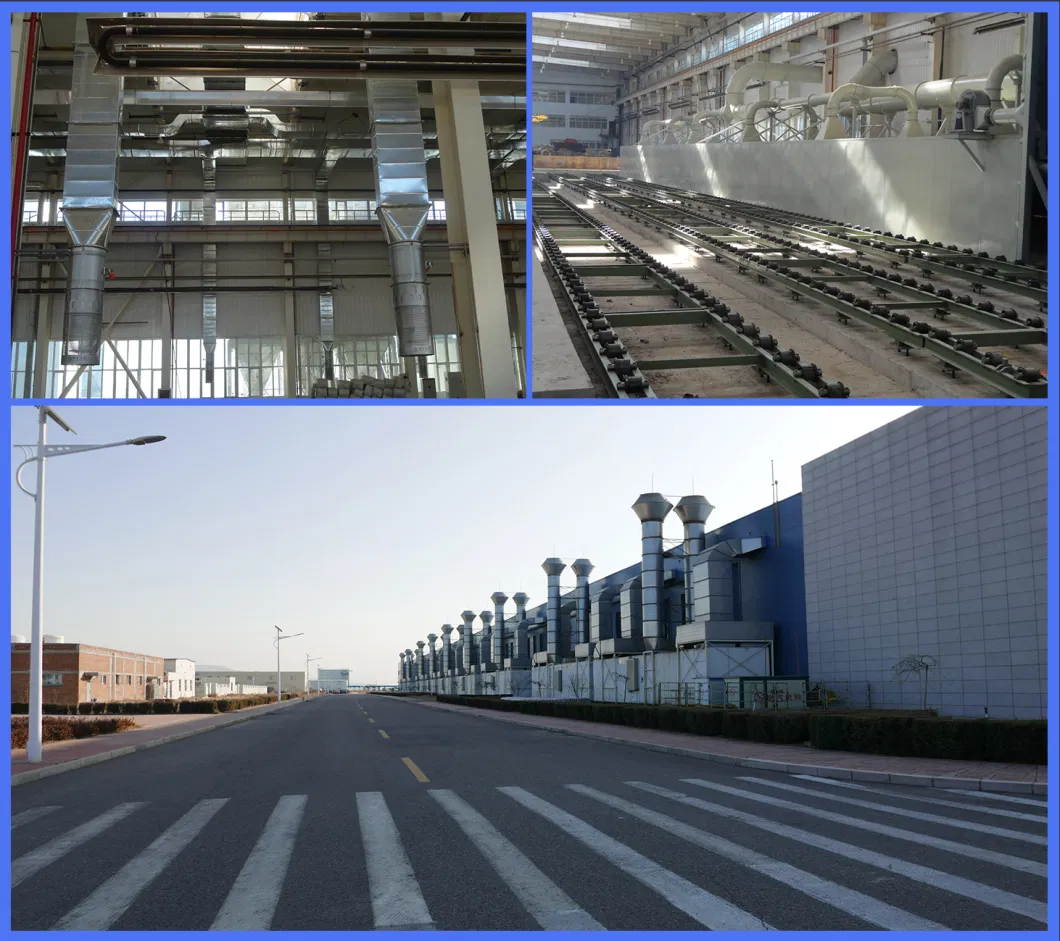